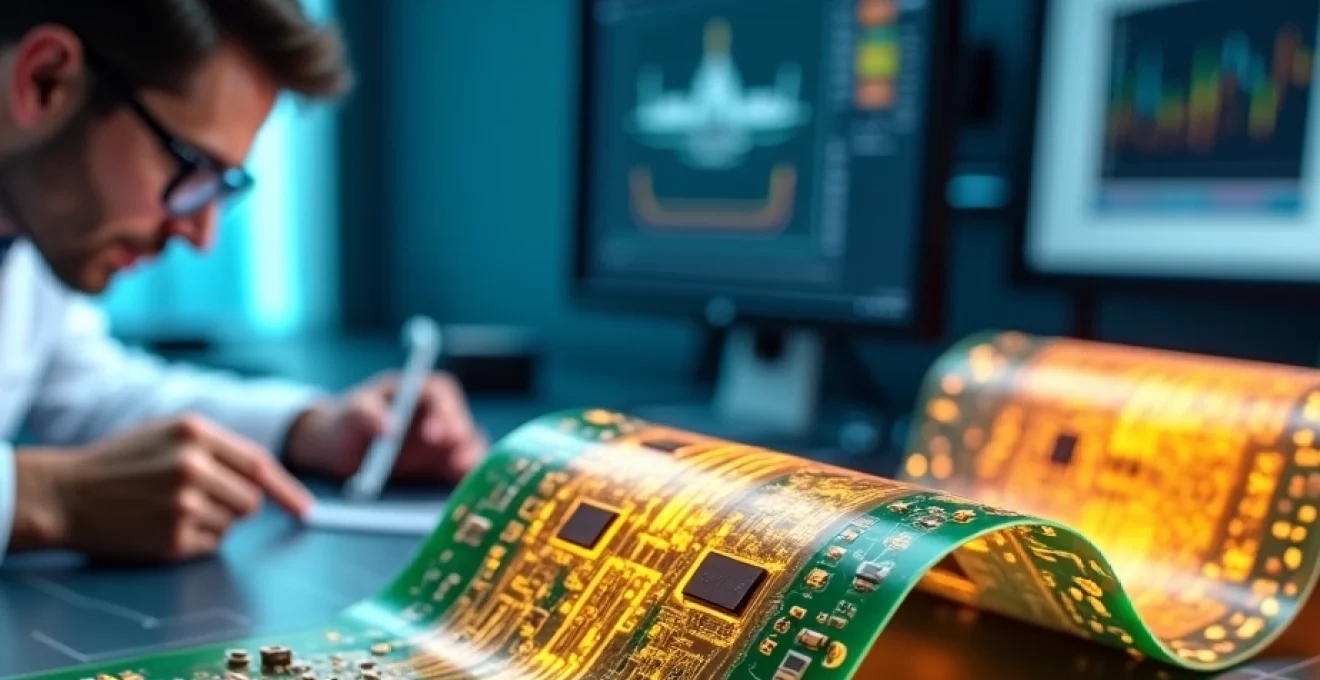
Nel mondo dell’elettronica moderna, la richiesta di soluzioni compatte, efficienti e versatili è in continua crescita. I circuiti stampati rigido-flessibili rappresentano una delle innovazioni più significative degli ultimi anni, combinando le caratteristiche di robustezza dei PCB tradizionali con la flessibilità necessaria per le applicazioni più complesse. Questi substrati ibridi stanno rivoluzionando il modo in cui vengono progettati i dispositivi elettronici, permettendo configurazioni tridimensionali prima impossibili con le tecnologie convenzionali.
La tecnologia rigido-flessibile offre un approccio integrato che elimina la necessità di connettori separati e cablaggi tra diverse schede rigide, riducendo così i potenziali punti di guasto e aumentando l’affidabilità complessiva del sistema. Con l’evoluzione dell’elettronica verso dispositivi sempre più piccoli e complessi, la capacità di integrare sezioni rigide e flessibili in un unico substrato è diventata fondamentale per molti settori industriali.
La crescente adozione di questa tecnologia è guidata non solo dalle esigenze di miniaturizzazione, ma anche dalla ricerca di soluzioni più durevoli ed efficienti dal punto di vista energetico. L’integrazione di substrati rigidi e flessibili in un’unica struttura rappresenta un compromesso ottimale tra prestazioni elettriche, resistenza meccanica e adattabilità alle forme complesse richieste dai moderni dispositivi elettronici.
Vantaggi dei PCB rigido-flessibili per l’elettronica moderna
I circuiti stampati rigido-flessibili offrono numerosi benefici rispetto ai tradizionali PCB rigidi o completamente flessibili, posizionandosi come soluzione ideale per applicazioni che richiedono sia robustezza che adattabilità. La loro struttura ibrida consente di sfruttare i punti di forza di entrambe le tecnologie, eliminando al contempo i rispettivi svantaggi. Per comprendere meglio i vantaggi di questa tecnologia avanzata, clicca qui per informazioni dettagliate.
La vera forza dei PCB rigido-flessibili risiede nella loro capacità di combinare zone rigide, ideali per il montaggio di componenti e connettori, con aree flessibili che permettono il movimento e l’adattamento a spazi tridimensionali complessi. Questa caratteristica unica consente di progettare dispositivi elettronici con forme non convenzionali, ottimizzando lo spazio disponibile e riducendo il numero di interconnessioni necessarie.
L’integrazione di sezioni rigide e flessibili in un unico substrato rappresenta uno dei più significativi avanzamenti nella tecnologia dei circuiti stampati degli ultimi decenni, permettendo configurazioni tridimensionali che prima richiedevano molteplici PCB interconnessi.
Maggiore densità di componenti e interconnessioni
Uno dei vantaggi più significativi dei PCB rigido-flessibili è la possibilità di ottenere una densità di componenti e interconnessioni notevolmente superiore rispetto ai circuiti tradizionali. La tecnologia rigid-flex
permette di distribuire i componenti su diverse aree rigide interconnesse da sezioni flessibili, consentendo un utilizzo ottimale dello spazio tridimensionale disponibile all’interno del dispositivo.
Questa configurazione elimina la necessità di connettori tra schede separate, permettendo di recuperare lo spazio che sarebbe stato occupato dai connettori stessi e dal volume necessario per il loro montaggio. In applicazioni dove ogni millimetro quadrato è prezioso, come nei dispositivi medici impiantabili o nell’elettronica indossabile, questa caratteristica risulta particolarmente vantaggiosa.
Inoltre, la riduzione del numero di connettori e saldature diminuisce significativamente i potenziali punti di guasto del sistema. Secondo recenti studi nel settore dell’elettronica, circa il 60% dei guasti nei dispositivi elettronici è attribuibile a problemi di interconnessione, rendendo l’approccio rigido-flessibile una soluzione efficace per aumentare l’affidabilità complessiva.
Migliore dissipazione del calore e affidabilità
I PCB rigido-flessibili offrono vantaggi significativi in termini di gestione termica rispetto ai tradizionali circuiti stampati. La combinazione di substrati con diverse proprietà termiche permette di ottimizzare la dissipazione del calore generato dai componenti elettronici, contribuendo a migliorare le prestazioni e la durata del dispositivo.
Le sezioni rigide, tipicamente realizzate con materiali ad alta conducibilità termica come FR-4 modificato o ceramiche avanzate, possono essere ottimizzate per dissipare efficacemente il calore generato dai componenti di potenza. Al contempo, le aree flessibili, generalmente costruite con poliimmidi resistenti alle alte temperature, possono sopportare condizioni termiche estreme senza degradarsi.
L’affidabilità dei PCB rigido-flessibili è ulteriormente migliorata dalla riduzione delle interconnessioni fisiche tra le diverse parti del circuito. Eliminando connettori e cablaggi separati, questi circuiti integrati riducono drasticamente i potenziali punti di guasto, aumentando la resistenza a vibrazioni, urti e cicli termici. Dati di settore indicano che i sistemi basati su tecnologia rigido-flessibile possono offrire un incremento dell’affidabilità fino al 40% rispetto a soluzioni equivalenti realizzate con PCB rigidi interconnessi.
Riduzione del peso e delle dimensioni
Uno dei benefici più immediati dell’utilizzo di PCB rigido-flessibili è la significativa riduzione del peso e delle dimensioni complessive del dispositivo elettronico. Eliminando la necessità di connettori separati, supporti meccanici e cablaggi aggiuntivi, questi circuiti integrati permettono di costruire dispositivi notevolmente più compatti e leggeri.
In settori come l’aerospaziale o il medicale, dove ogni grammo risparmiato ha un impatto significativo, i PCB rigido-flessibili possono portare a riduzioni di peso fino al 60% rispetto a soluzioni equivalenti realizzate con tecnologie tradizionali. Questo si traduce direttamente in maggiore efficienza energetica, autonomia prolungata per i dispositivi a batteria e minori costi operativi.
La miniaturizzazione permessa da questa tecnologia non comporta compromessi in termini di funzionalità. Al contrario, la possibilità di distribuire i componenti su diverse aree rigide interconnesse da sezioni flessibili consente spesso di implementare funzionalità aggiuntive all’interno dello stesso ingombro, aumentando il valore e le capacità del prodotto finale.
Applicazioni dei PCB rigido-flessibili in diversi settori
La versatilità dei circuiti stampati rigido-flessibili ha portato alla loro adozione in numerosi settori industriali, dove le esigenze di miniaturizzazione, affidabilità e adattabilità sono particolarmente critiche. Questi substrati ibridi trovano applicazione in contesti estremamente diversificati, dalla medicina all’aerospaziale, dall’elettronica di consumo all’automotive di alta gamma.
La crescente domanda di dispositivi elettronici più compatti, leggeri e affidabili ha accelerato l’adozione della tecnologia rigido-flessibile, con un tasso di crescita annuale stimato intorno al 12-15% secondo le più recenti analisi di mercato. Questa tendenza è destinata a rafforzarsi ulteriormente con l’evoluzione delle tecniche di fabbricazione e la riduzione dei costi di produzione.
Dispositivi medici compatti e indossabili
Il settore medicale rappresenta uno degli ambiti applicativi più promettenti per i PCB rigido-flessibili, grazie alle stringenti esigenze di miniaturizzazione, biocompatibilità e affidabilità. I dispositivi medici impiantabili, come pacemaker, neurostimolatori e pompe per infusione, beneficiano enormemente della capacità di questi circuiti di adattarsi all’anatomia umana, riducendo al minimo l’ingombro e massimizzando il comfort del paziente.
Anche nel campo dei dispositivi indossabili per il monitoraggio dei parametri vitali, i PCB rigido-flessibili offrono vantaggi considerevoli. La possibilità di distribuire i sensori e l’elettronica di elaborazione su diverse aree rigide, mantenendole interconnesse tramite sezioni flessibili, permette di realizzare dispositivi confortevoli, leggeri e resistenti ai movimenti quotidiani del paziente.
Un esempio emblematico è rappresentato dai moderni sistemi di monitoraggio continuo del glucosio, dove la tecnologia rigido-flessibile ha permesso di ridurre le dimensioni del dispositivo del 40% nell’ultimo decennio, aumentando contemporaneamente l’autonomia della batteria e la precisione delle misurazioni. Questa evoluzione è stata resa possibile proprio dalla capacità di integrare sensori, processori e sistemi di comunicazione in un unico substrato tridimensionale ottimizzato.
Elettronica aerospaziale resistente a vibrazioni
Nel settore aerospaziale, dove affidabilità e resistenza a condizioni estreme sono requisiti imprescindibili, i PCB rigido-flessibili hanno trovato numerose applicazioni di successo. L’ambiente spaziale presenta sfide uniche, tra cui vibrazioni intense durante il lancio, escursioni termiche estreme e radiazioni ionizzanti, che mettono a dura prova qualsiasi sistema elettronico.
I circuiti rigido-flessibili, grazie alla loro struttura integrata priva di interconnessioni meccaniche fragili, offrono una resistenza superiore alle vibrazioni rispetto ai tradizionali PCB rigidi interconnessi. Le sezioni flessibili consentono inoltre di assorbire le dilatazioni termiche differenziali, riducendo il rischio di rotture dovute ai cicli termici tipici dell’ambiente spaziale.
Nei moderni satelliti di telecomunicazione, l’adozione di PCB rigido-flessibili ha permesso di ridurre il peso dei sistemi elettronici fino al 40%, con un impatto significativo sui costi di lancio (stimati in circa 10.000-20.000 dollari per chilogrammo). Contemporaneamente, l’affidabilità complessiva è aumentata, con una riduzione dei tassi di guasto stimata intorno al 35% rispetto alle soluzioni tradizionali.
Smartphone pieghevoli e dispositivi wearable
L’elettronica di consumo rappresenta uno dei mercati in più rapida espansione per i PCB rigido-flessibili, con applicazioni innovative che spaziano dagli smartphone pieghevoli agli smartwatch, dagli auricolari wireless ai dispositivi per la realtà aumentata. In tutti questi ambiti, la capacità di combinare aree rigide per il montaggio dei componenti con sezioni flessibili per le interconnessioni e l’adattabilità alle forme è cruciale.
Gli smartphone pieghevoli, una delle innovazioni più recenti nel mercato consumer, si basano pesantemente sulla tecnologia rigido-flessibile per realizzare la zona di cerniera che deve sopportare decine di migliaia di cicli di apertura e chiusura. In questo contesto, i PCB rigido-flessibili non solo permettono il movimento fisico necessario, ma anche un’eccellente integrità del segnale attraverso l’area di piegatura, aspetto fondamentale per garantire prestazioni elevate del display e dei sensori.
Anche i moderni smartwatch e tracker fitness beneficiano enormemente di questa tecnologia. La forma ergonomica di questi dispositivi, progettati per adattarsi perfettamente al polso, richiede soluzioni elettroniche capaci di conformarsi a superfici curve. I PCB rigido-flessibili permettono di distribuire i componenti elettronici attorno al polso, ottimizzando il comfort e aumentando lo spazio disponibile per batterie più capienti o sensori aggiuntivi.
I dispositivi elettronici di nuova generazione richiedono soluzioni circuitali non convenzionali, capaci di adattarsi a forme tridimensionali complesse mantenendo al contempo elevate prestazioni elettriche e affidabilità meccanica.
Considerazioni di progettazione per PCB rigido-flessibili
La progettazione di circuiti rigido-flessibili richiede un approccio sostanzialmente diverso rispetto ai tradizionali PCB rigidi. Le considerazioni non si limitano agli aspetti puramente elettrici, ma devono necessariamente includere fattori meccanici, termici e di producibilità che possono influenzare significativamente le prestazioni e l’affidabilità del prodotto finale.
Un aspetto fondamentale nella progettazione di questi circuiti è la definizione precisa delle aree rigide e flessibili, con particolare attenzione alle zone di transizione tra le due tipologie di substrato. Queste aree rappresentano infatti i punti più critici del circuito, dove possono concentrarsi stress meccanici potenzialmente dannosi per l’integrità delle tracce conduttive.
Scelta dei materiali flessibili adeguati
La selezione dei materiali appropriati rappresenta uno degli aspetti più critici nella progettazione di PCB rigido-flessibili. Le sezioni flessibili richiedono substrati con caratteristiche meccaniche ed elettriche specifiche, in grado di sopportare ripetuti cicli di flessione senza compromettere l’integrità delle tracce conduttive. Il poliimmide (PI) rimane il materiale più diffuso per queste applicazioni, grazie alla sua eccellente resistenza meccanica, stabilità dimensionale e caratteristiche termiche.
La scelta dello spessore del substrato flessibile influenza direttamente il raggio minimo di curvatura che il circuito potrà sopportare senza danneggiamenti. In generale, substrati più sottili consentono raggi di curvatura minori, ma possono presentare sfide in termini di manipolazione durante il processo produttivo e resistenza meccanica nel prodotto finale. I progettisti devono bilanciare attentamente queste esigenze, considerando anche il numero di strati conduttivi necessari nelle aree flessibili.
Anche la selezione del materiale conduttivo richiede particolare attenzione. Il rame elettrolitico standard, ampiamente utilizzato nei PCB rigidi, può risultare inadeguato per applicazioni che richiedono flessioni ripetute, a causa della sua tendenza a sviluppare microfratture con l’uso prolungato. In questi casi, il rame rolled-annealed (RA), caratterizzato da una struttura granulare più fine e uniforme, offre una resistenza alla fatica meccanica significativamente superiore, giustificando il suo costo più elevato in applicazioni critiche.
Ottimizzazione del layout per la flessibilità
La progettazione del layout di un PCB rigido-flessibile richiede un’attenzione particolare alla disposizione delle tracce nelle aree destinate alla flessione. A differenza dei circuiti rigidi tradizionali, dove le considerazioni sono prevalentemente elettriche, in questo caso gli aspetti meccanici assumono un’importanza fondamentale per garantire l’affidabilità a lungo termine del prodotto.
Una regola basilare consiste nel disporre le tracce conduttive perpendicolarmente alla linea di piegatura, riducendo così lo stress meccanico a cui sono sottoposte durante la flessione. Quando questa configurazione non è possibile, è consigliabile utilizzare tracce con curve dolci o a forma di “S” che possano distribuire lo stress su un’area più ampia, piuttosto che angoli a 90° che tendono a concentrare le tensioni meccaniche in punti specifici.
Lo spessore e la larghezza delle tracce nelle aree flessibili meritano particolare attenzione. Tracce più sottili e larghe offrono generalmente una maggiore resistenza ai cicli di flessione ripetuti. Alcuni progettisti adottano la tecnica del dual-thickness copper
, utilizzando rame più spesso nelle aree rigide per ottimizzare la conducibilità elettrica e rame più sottile nelle zone flessibili per migliorarne le caratteristiche meccaniche. È inoltre fondamentale evitare transizioni brusche di larghezza delle tracce nelle aree soggette a flessione, preferendo variazioni graduali che riducano la concentrazione degli stress.
Test di affidabilità e durata meccanica
La validazione dell’affidabilità e della durata meccanica rappresenta una fase cruciale nello sviluppo di PCB rigido-flessibili, soprattutto per applicazioni dove il circuito sarà sottoposto a movimenti ripetuti durante il suo ciclo di vita. I test di piegatura ciclica, che simulano le condizioni operative reali, permettono di identificare potenziali punti deboli del design prima che il prodotto entri in produzione.
Per applicazioni statiche, dove il circuito viene piegato solo durante l’installazione, possono essere sufficienti test semplificati che verifichino l’integrità elettrica dopo un numero limitato di cicli di flessione. Per dispositivi come smartphone pieghevoli o cerniere di laptop, invece, i test devono simulare migliaia o addirittura milioni di cicli, utilizzando apparecchiature specializzate che riproducano esattamente il raggio di curvatura e le condizioni meccaniche previste nell’applicazione finale.
Oltre ai test meccanici, è fondamentale sottoporre i prototipi a verifiche ambientali che simulino le condizioni operative previste, inclusi cicli termici, umidità e, quando necessario, esposizione a sostanze chimiche o radiazioni. La combinazione di stress meccanici e ambientali può rivelare vulnerabilità non evidenti con test singoli, permettendo di ottimizzare il design per massimizzare l’affidabilità complessiva del prodotto finale.
Processo di fabbricazione dei PCB rigido-flessibili
Il processo produttivo dei circuiti stampati rigido-flessibili è significativamente più complesso rispetto a quello dei tradizionali PCB rigidi, richiedendo tecniche specializzate e controlli di qualità più rigorosi. La complessità deriva principalmente dalla necessità di integrare materiali con caratteristiche fisiche diverse e garantire transizioni affidabili tra le sezioni rigide e flessibili.
La fabbricazione di questi circuiti ibridi richiede un’attenta pianificazione e controllo di ciascuna fase del processo, dalla preparazione dei materiali di base fino all’ispezione finale. Ogni passaggio deve essere ottimizzato per tenere conto delle particolari caratteristiche dei substrati flessibili, che reagiscono in modo diverso rispetto ai materiali rigidi tradizionali durante le varie fasi di lavorazione.
Le tecnologie di produzione per i PCB rigido-flessibili continuano ad evolversi, con innovazioni che mirano a migliorare l’affidabilità delle interconnessioni, ridurre i tempi di processo e minimizzare i costi complessivi. Queste evoluzioni stanno rendendo la tecnologia rigido-flessibile sempre più accessibile anche per progetti con budget limitati, ampliandone ulteriormente il campo di applicazione.
Laminazione multistrato di substrati rigidi flessibili
Il processo di laminazione rappresenta una delle fasi più critiche nella produzione di PCB rigido-flessibili. A differenza dei PCB rigidi tradizionali, dove tutti i materiali rispondono in modo simile alla pressione e al calore, la laminazione di substrati con caratteristiche fisiche diverse richiede un controllo preciso dei parametri di processo per evitare problemi come delaminazioni, spostamenti degli strati o deformazioni.
Un aspetto particolarmente delicato riguarda l’utilizzo di prepreg “no-flow” o a flusso controllato nelle aree di transizione tra le sezioni rigide e flessibili. Questi materiali speciali permettono di creare un legame solido nelle aree rigide senza che la resina fluisca nelle sezioni flessibili, dove potrebbe compromettere la flessibilità e la durata del circuito. La precisione nel posizionamento di questi materiali e nel controllo dei parametri di laminazione (temperatura, pressione e tempo) è fondamentale per ottenere risultati consistenti.
Per circuiti multistrato complessi, il processo di laminazione può essere suddiviso in più fasi, con laminazioni parziali e successive lavorazioni intermedie. Questa approccio, sebbene più costoso e complesso, permette di ottenere strutture stratificate con un maggiore controllo dell’allineamento tra i vari strati e migliori prestazioni meccaniche nelle aree di transizione. In alcuni casi, vengono utilizzati materiali sacrificali o distanziatori temporanei per proteggere le aree flessibili durante la laminazione, rimuovendoli successivamente nelle fasi finali del processo.
Tecniche di interconnessione tra sezioni rigide
Le interconnessioni tra le sezioni rigide e flessibili rappresentano uno degli aspetti più critici nella realizzazione di PCB rigido-flessibili affidabili. Queste aree di transizione sono soggette a stress meccanici concentrati che possono compromettere l’integrità delle connessioni elettriche, richiedendo quindi tecniche specializzate per garantirne l’affidabilità a lungo termine.
Una soluzione ampiamente adottata consiste nell’utilizzo di “tear drops” o raccordi a goccia nelle connessioni tra pad e tracce nelle aree di transizione. Questa configurazione distribuisce lo stress meccanico su un’area più ampia, riducendo il rischio di rotture nelle tracce conduttive. In modo simile, l’adozione di raggi di curvatura generosi per le tracce che attraversano la zona di transizione contribuisce a minimizzare le concentrazioni di stress.
Per applicazioni ad alta affidabilità, è comune l’impiego di tecniche di rinforzo meccanico nelle aree di transizione. Questi rinforzi possono includere l’applicazione di materiali adesivi flessibili o l’utilizzo di strutture meccaniche dedicate che limitano il movimento nelle immediate vicinanze della transizione, proteggendo le interconnessioni elettriche da sollecitazioni eccessive. In alcuni casi, vengono implementate ridondanze nei collegamenti critici, con percorsi paralleli che garantiscono la continuità elettrica anche in caso di guasto parziale di una connessione.
Costi e tempi di sviluppo dei PCB rigido-flessibili
L’adozione della tecnologia rigido-flessibile comporta considerazioni economiche e temporali specifiche che devono essere attentamente valutate nella pianificazione di un progetto. Sebbene i costi iniziali siano generalmente superiori rispetto alle soluzioni basate su PCB rigidi tradizionali, un’analisi completa del ciclo di vita del prodotto spesso rivela vantaggi economici significativi nel medio-lungo termine.
I tempi di sviluppo per progetti basati su PCB rigido-flessibili tendono ad essere più estesi, principalmente a causa della maggiore complessità nella progettazione e nella validazione. La necessità di considerare aspetti meccanici, elettrici e termici in modo integrato richiede iterazioni progettuali più numerose e approfonditĀ, con frequente ricorso a simulazioni multifisiche e prototipi funzionali.
È fondamentale considerare che, mentre i costi di produzione unitari rimangono più elevati rispetto ai PCB rigidi convenzionali, i risparmi derivanti dall’eliminazione di connettori, cablaggi e schede separate possono compensare significativamente questa differenza. Inoltre, i benefici in termini di affidabilità, miniaturizzazione e prestazioni complessive spesso giustificano l’investimento iniziale maggiore, soprattutto per prodotti di fascia alta o applicazioni critiche.
Fattori che influenzano i costi di produzione
I costi di produzione dei PCB rigido-flessibili sono influenzati da numerosi fattori, alcuni comuni ai tradizionali PCB rigidi e altri specifici di questa tecnologia. La complessità del design rappresenta uno dei principali driver di costo, con parametri come il numero di strati, la densità delle interconnessioni e la precisione richiesta che impattano significativamente sul prezzo finale.
I materiali costituiscono una componente sostanziale del costo complessivo. I substrati flessibili in poliimmide, i prepreg speciali “no-flow” e il rame rolled-annealed hanno prezzi significativamente più elevati rispetto ai materiali standard utilizzati nei PCB rigidi. Per progetti con vincoli di budget severi, è fondamentale valutare attentamente la reale necessità di materiali premium in tutte le aree del circuito, limitandone l’uso alle zone dove le loro caratteristiche sono effettivamente indispensabili.
Anche i volumi di produzione influenzano in modo determinante i costi unitari. Per piccole serie o prototipi, l’incidenza dei costi di attrezzaggio e setup è particolarmente elevata, rendendo la tecnologia rigido-flessibile relativamente costosa. Con l’aumentare dei volumi, questi costi fissi vengono ammortizzati su un numero maggiore di unità, riducendo l’impatto sul costo del singolo pezzo. Per questo motivo, l’approccio rigido-flessibile risulta particolarmente vantaggioso per prodotti destinati a produzioni di medio-grande serie.
Ottimizzazione del design per ridurre i costi
Un design ottimizzato può ridurre significativamente i costi di produzione dei PCB rigido-flessibili senza compromettere le funzionalità essenziali. Approcci come la standardizzazione delle aree flessibili, limitando il numero di configurazioni diverse all’interno dello stesso circuito, possono semplificare il processo produttivo e ridurre gli scarti, con conseguenti benefici economici.
La razionalizzazione del numero di strati rappresenta un’altra strategia efficace per il contenimento dei costi. Ogni strato aggiuntivo aumenta non solo il costo dei materiali, ma anche la complessità del processo di laminazione e le probabilità di difetti. Un’attenta analisi dei requisiti elettrici e meccanici può spesso portare a soluzioni con un numero ridotto di strati che mantengono le prestazioni necessarie con costi produttivi inferiori.
L’ottimizzazione dell’imposition (disposizione dei circuiti sul pannello di produzione) rappresenta un aspetto spesso sottovalutato ma con potenziale impatto significativo sui costi, soprattutto per produzioni in serie. Massimizzare il numero di circuiti realizzabili da ciascun pannello, tenendo conto delle limitazioni imposte dalle aree flessibili, può ridurre sensibilmente il costo unitario. La collaborazione precoce con il produttore durante la fase di design può portare a soluzioni ottimizzate che bilanciano efficacemente i panel yield
con i requisiti funzionali del circuito.
Tempistiche tipiche per prototipi e produzione
La pianificazione realistica delle tempistiche di sviluppo è fondamentale per il successo di progetti basati su PCB rigido-flessibili. Il ciclo di sviluppo di questi circuiti è generalmente più lungo rispetto ai tradizionali PCB rigidi, richiedendo fasi aggiuntive sia nella progettazione che nella validazione. Per prototipi di media complessità, è consigliabile prevedere 2-4 settimane aggiuntive rispetto ai tempi standard dei PCB convenzionali.
La fase di progettazione richiede particolare attenzione, con tempistiche che possono variare da 1-2 settimane per design relativamente semplici fino a 6-8 settimane per progetti complessi multistrato con requisiti meccanici ed elettrici stringenti. È fortemente consigliabile includere nel cronoprogramma sessioni di revisione del design con il produttore selezionato, che può fornire feedback preziosi sulla producibilità e suggerire modifiche che potrebbero ridurre significativamente costi e tempi di realizzazione.
La produzione dei prototipi rappresenta un’altra fase critica, con tempistiche che dipendono dalla complessità del design e dalle capacità del fornitore. Per PCB rigido-flessibili standard, i tempi tipici variano da 3 a 5 settimane, mentre configurazioni particolarmente complesse possono richiedere fino a 8-10 settimane. È importante notare che, a differenza dei PCB rigidi dove i servizi di prototipazione rapida possono offrire consegne in 24-48 ore, per i circuiti rigido-flessibili le opzioni di “quick-turn” sono significativamente più limitate e generalmente più costose.
Per quanto riguarda la produzione in serie, dopo l’approvazione dei prototipi, i tempi di approvvigionamento si stabilizzano generalmente tra le 4 e le 6 settimane per lotti standard, con possibilità di riduzioni per ordini programmati e ricorrenti. La creazione di partnership strategiche con fornitori specializzati può contribuire significativamente a ottimizzare questi tempi, specialmente per prodotti con cicli di vita estesi.